Grüne Sterne: Nachhaltige Materialien bei Mercedes – ein Interview mit Dr. Ulf Zillig
23. Januar 2023 von Irene Wallner
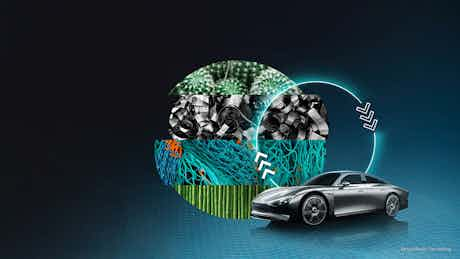
Nachhaltigkeit in der Automobilbranche wird immer wichtiger. Dabei reicht es nicht mehr aus, sich in Sachen Elektromobilität weiterzuentwickeln. Ein ganzheitlich nachhaltiger Ansatz muss geschaffen werden. Mercedes und die Tochterfirma AMG sind Hersteller, die beim Thema nachhaltige Materialien schon einige Forschungsprojekte gestartet haben. Erfahren Sie in diesem Interview, welche Zukunftsmaterialien zum Einsatz kommen könnten.
Wir haben bei Dr. Ulf Zillig, dem Leiter für Konzernforschung & Nachhaltigkeit, nachgefragt.
Ressourcenschonend verarbeitetes Echtleder wird ab 2023 sukzessive auf alle Baureihen ausgerollt. Was bedeutet ressourcenschonend in diesem Zusammenhang genau? Und ganz allgemein: Warum setzt man überhaupt noch auf Echtleder?
UZ: Beim Thema Nachhaltigkeit gehen wir bei Mercedes-Benz ganzheitlich vor – bei allen Materialien und Bauteilen. Der Innenraum unserer Fahrzeuge ist dabei eine wichtige Schnittstelle zu unseren Kunden, über die sie unsere Produkte direkt erleben. Leder steht aufgrund seiner Haptik, Optik und Langlebigkeit seit jeher für Qualität und eine hohe Wertigkeit – ein Anspruch, den wir auch an unsere Fahrzeuge haben.
Wir wollen unseren Kunden daher beides bieten: Lederalternativen für die, die kein Leder wünschen. Und den Kunden, die eine Lederausstattung schätzen, möchten wir dies auch ermöglichen – aber auf eine nachhaltigere Art und Weise.
Deshalb bieten wir in unseren Autos ab 2023 Schritt für Schritt nur noch Leder an, das nachhaltig erzeugt und verarbeitet wurde. Wir betrachten dabei unterschiedliche Nachhaltigkeitsaspekte wie Tierwohl, Transparenz in der Lieferkette und die Umweltauswirkungen des Gerbprozesses. Unsere Lieferanten dürfen beispielsweise bei der Gerbung künftig nur noch pflanzliche oder alternative nachhaltige Gerbstoffe einsetzen, die keinerlei Chrom enthalten.
Diese Alternativen werden z.B. aus Schalen von Kaffeebohnen oder Kastanien hergestellt. Mit unseren Partnern arbeiten wir zudem daran, den ökologischen Fußabdruck des Leders weiter zu verbessern, etwa durch die Reduzierung von Wasser, Energie und Chemikalien im Gerbprozess.
Nachwachsende Rohstoffe wie Kaktusfasern, Pilzmyzelien usw. wären Alternativen zu Leder. Wie weit sind diese Forschungen, wann könnte das erste Modell mit einer dieser Alternativen auf den Markt kommen?
UZ: Das ist ein wichtiges und innovatives Feld, mit dem wir uns in der Konzernforschung beschäftigen: Wir untersuchen unterschiedliche Materialien und Textilien als Alternative zu Echtleder für einen möglichen Einsatz im Fahrzeuginnenraum. Die Produkte müssen allerdings nicht nur unseren Nachhaltigkeitsanforderungen, sondern auch unseren hohen technischen Anforderungen an die Mercedes-Benz Spitzenqualität gerecht werden. Daher prüfen wir sehr genau, welche Materialien sich letztlich für den Einsatz im Fahrzeug eignen.
Auch Faktoren wie Langlebigkeit und nicht zuletzt Optik, Haptik, Funktionalität und Komfort spielen dabei eine Rolle. Nehmen wir den Fahrzeuginnenraum als Beispiel: Oberflächenmaterialien müssen extremen Temperaturen, Sonnenlicht, Abrieb von Jeanshosen und am Lenkrad Produkten wie Desinfektionsmitteln oder Sonnencreme standhalten – und das über einen langen Zeitraum hinweg. Nur wenn ein Werkstoff diesen Anforderungen standhält, kommt er für den Einsatz im Fahrzeug infrage.
Welcher Rohstoff ist der vielversprechendste, und warum? Was sind Probleme mit anderen Rohstoffen?
UZ: Es gibt einige spannende Produkte, die in unseren Fahrzeugen als potenzielle Materialien der Zukunft eingesetzt werden könnten. Einige davon haben wir 2022 in unserem Technologieprogramm, dem Mercedes-Benz VISION EQXX, vorgestellt. Dazu gehören beispielsweise Lederalternativen auf Basis von Naturfasern. Das Besondere daran ist, dass es sich dabei um völlig neue Materialkategorien handelt, die teilweise biotechnologisch im Labor entstehen.
Grundsätzlich ist es aber so, dass die Anforderungen für den Einsatz von Materialien im Automobilbereich sehr hoch sind. Das Material muss zum Beispiel Temperaturunterschieden von rund 100 Grad standhalten, ohne instabil zu werden, Gerüche abzusondern oder sich zu verfärben. In Punkto Nachhaltigkeit sind die Grenzen für uns unter anderem da gegeben, wo ein alternativer Werkstoff Monokulturen unterstützen würde, die negative Auswirkungen auf unsere Umwelt und das Ökosystem haben könnten.
Ist es zukünftig möglich, ein Mercedes-Modell komplett aus ressourcenschonenden und nachwachsenden Rohstoffen zu fertigen?
UZ: Nachhaltigkeit ist ein Leitmotiv all unserer Forschungs- und Entwicklungsaktivitäten bei Mercedes-Benz. Der Ansatz, den wir dabei verfolgen, nennt sich „Design for Environment“. Das bedeutet, dass wir schon in der Konzeptionsphase eines Fahrzeugs alle Teile und Materialien überdenken und Möglichkeiten für nachhaltigere Alternativen prüfen. Das gilt nicht nur für Oberflächenmaterialien im Fahrzeuginnenraum, sondern auch für Materialien, die für den Kunden nicht sichtbar sind.
Ein schönes Beispiel für dieses ganzheitliche Vorgehen sind die Kabelkanäle aus einem Kunststoffersatzmaterial, das aus upgecycelten, unsortierten Haushaltsabfällen gewonnen wird. Sie kamen im EQS und EQE im Rahmen eines Serienpiloten 2022 erstmals zum Einsatz. Darüber hinaus haben wir recycelte Materialien im Fahrzeuginnenraum vieler Fahrzeuge bereits in Serie – z.B. in Polsterstoffen, die bis zu 100 % aus recycelten PET-Flaschen bestehen. Und auch in der Karosserie setzen wir Flachstahl ein, der im Elektrolichtbogenofen zu 100 % aus Schrott hergestellt wird und die CO2-Emissionen im Vergleich zur klassischen Hochofenroute um mehr als 60 % reduziert.
Das heißt aber nicht, dass wir damit schon am Ziel sind. Im nächsten Schritt wollen wir den Anteil von Sekundärrohstoffen in unserer Pkw-Flotte bis 2030 auf durchschnittlich 40 Prozent erhöhen.
Gibt es auch Überlegungen, wie man Elektroauto-Akkus ressourcenschonender herstellen will – und vor allem recyceln? Es gibt für das Recyceln von E-Auto-Akkus auch vielversprechende Ansätze mit Schimmelpilzen.
UZ: Auf dem Weg zu einem geschlossenen Wertstoffkreislauf ist das nachhaltige Batterierecycling ein wesentlicher Faktor, der zur Reduzierung des Ressourcenverbrauchs beiträgt. Bei Mercedes-Benz wollen wir beispielsweise 2023 am Standort Kuppenheim eine CO2-neutrale Pilotfabrik zum Recycling von Lithium-Ionen-Batterien in Betrieb nehmen. Nach vollständiger Inbetriebnahme können wir die Recyclingquote von Batteriematerialien am Standort auf mehr als 96 Prozent steigern. Die neue Pilotfabrik soll künftig die gesamte Prozesskette des Batterierecyclings abbilden: Von der Entwicklung von Logistikkonzepten, über das nachhaltige Recycling der wertvollen Rohstoffe bis hin zur Reintegration von Rezyklat in die Herstellung neuer Batterien.
Welcher Teil eines Fahrzeugs ist am schwierigsten mit ressourcenschonenden und/oder nachwachsenden Rohstoffen zu fertigen? Gerade Reifen sind schwer wiederverwertbar, hat Mercedes hier auch Ansätze?
UZ: Der Einsatz von Sekundärrohstoffen schien bisher insbesondere bei sicherheitsrelevanten und anspruchsvollen Bauteile eine Herausforderung zu sein, da diese keine Veränderung oder Abweichungen in ihren Materialeigenschaften tolerieren. Das hat sich zuletzt mit dem sogenannten „chemischen Recycling“ geändert. Dieses innovative Herstellungsverfahren ermöglicht uns, erstmals einen Recycling-Kunststoff einzusetzen, der exakt die gleichen Eigenschaften hat, wie ein Neukunststoff – und ganz nebenbei schließen wir auch noch den Wertstoffkreislauf.
Konkret haben wir gemeinsam mit BASF und dem Start-up Pyrum Innovations ein Projekt gestartet, bei dem ausgediente Autoreifen durch das Verfahren zu neuwertigen Kunststoffteilen werden, die wieder im Fahrzeug eingesetzt werden können – zum Beispiel in Form von Bügeltürgriffen.
Beim EQE und der S-Klasse bringen wir diese Teile schon dieses Jahr in Serie. Dafür werden die Altreifen bei unserem Partner Pyrum zunächst geschreddert und aus dem entstandenen Granulat ein Pyrolyse-Öl erzeugt. BASF kombiniert das Öl im nächsten Schritt mit Biomethan aus Landwirtschaftsabfällen und bildet damit den Ausgangstoff für einen neuen Kunststoff, der die gleichen Sicherheitsanforderungen erfüllt wie Primärmaterial und sich auch genauso gut lackieren lässt.
Er ist nach dem Massenbilanzverfahren zertifiziert. Dabei bestätigt eine unabhängige Zertifizierung, dass der Partner die für das Endprodukt benötigten Mengen an fossilen Ressourcen durch nachwachsende Rohstoffe und Pyrolyse-Öl aus recycelten Altreifen ersetzt hat. Bei gleichen Eigenschaften des Endprodukts schont das Verfahren fossile Ressourcen und verringert den CO2-Fußabdruck des Kunststoffs. Das Material eignet sich damit bestens für den Einsatz in Fahrzeugbauteilen.